Was ist ein MES?
Ein Manufacturing Execution System (MES) ist ein Fertigungsmanagementsystem, das als Verbindung zwischen der Fertigungsebene und der Unternehmensleitebene (ERP) dient. Es liefert die Abbildung der Produktion, indem Produktionsdaten erfasst und an das ERP-System weitergegeben werden. Es überwacht die Produktion und erkennt rechtzeitig mögliche Schwachstellen. Als ein bedeutender Bestandteil der digitalen Transformation, wird die Produktion transparent visualisiert und alle gesammelten und umfangreichen Daten können in einer Vielzahl verschiedener Kennzahlen ausgewertet werden.
Ein MES-System ist das operative Bindeglied zwischen der Maschinensteuerung (SCADA/SPS) und dem Unternehmensmanagement (dem ERP-System). Die Aufgaben unterteilen sich in unterschiedliche Themengebiete, insbesondere die Datenerfassung (BDE/MDE Betriebs- und Maschinendatenerfassung), Planung und Steuerung (APS/ grafische Plantafel), Leistungsanalyse (KPI/ OEE), Qualitätsmanagement (QS-System), Informationsmanagement (Visualisierung), Energiemanagement (als Grundlage für ISO 50001), Betriebsmittelmanagement und Auftragsmanagement.
Wir gehen mit Ihnen den Weg zur Smart Factory
Gemäß Industrie 4.0 sollen alle Informationen der Wertschöpfungskette zu jeder Zeit und an jedem Ort verfügbar und aktuell sein. Mit der MES Suite PROefficient werden Betriebs- und Maschinendaten mit intelligenter Soft- und Hardware vernetzt und liefern in Echtzeit relevante Informationen, Auswertungen und Kennzahlen. Unser ausgesprochenes Ziel ist es, die Informationen in immer weitere Bereiche der Wertschöpfungskette zu integrieren, weshalb wir täglich an der Weiterentwicklung von hochinnovativen Lösungen gemeinsam mit unseren Kunden arbeiten.
Erfolge in Ihrer Abteilung
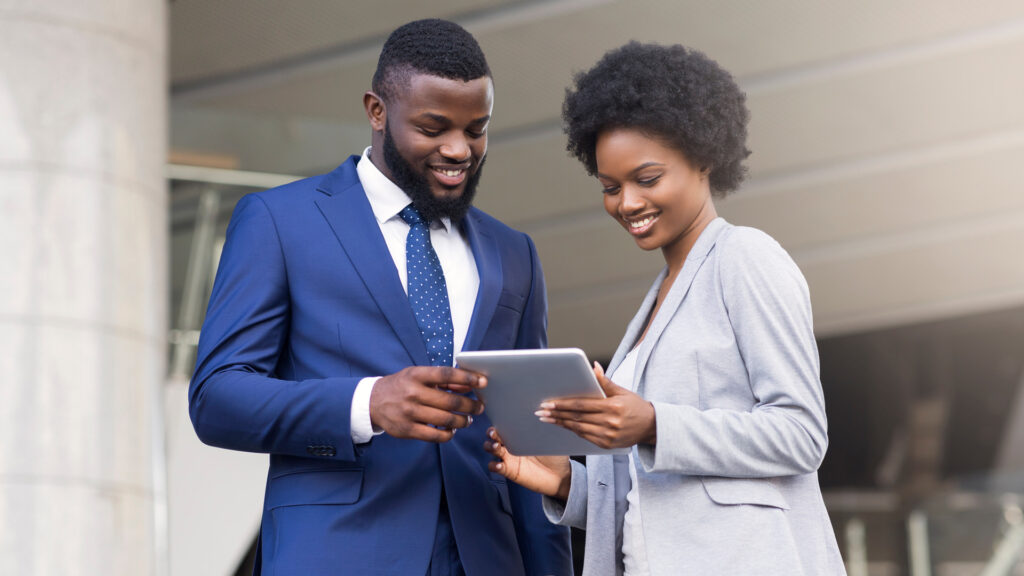
Unternehmensleitung
Unser MES-System liefert die Grundlage für fundierte Entscheidungen, die Ihre Produktion betreffen. Durchgängige Auftragsrückmeldungen und Bestandsbuchungen führen zu Transparenz auf Produkt- und Arbeitsplatzebene, ermöglichen eine genauen Kalkulation der Herstellungskosten, helfen die Materialbestände zu optimieren und bilden die Basis für ein Kennzahlensystem zur Beurteilung der Effizienz und Produktivität.

Produktionsleitung
Für Sie als Produktionsleiter steht Transparenz im Vordergrund. Sie wollen nicht unnötige Zeit mit Informationsbeschaffung vergeuden. Nur wer Informationen jederzeit live im Blick hat, kann Entscheidungen treffen. Die erfassten Daten aus BDE und MDE werden ONLINE visualisiert und fließen in einem Kennzahlensystem zusammen. Sie geben Ihnen Aufschluss über das aktuelle Produktionsgeschehen. Sie sind in der Lage einzelne Arbeitsplätze und Maschinen anhand ihrer KPIs, z. B. OEE zu vergleichen und zu beurteilen sowie Prozessverluste übergreifend zu analysieren.
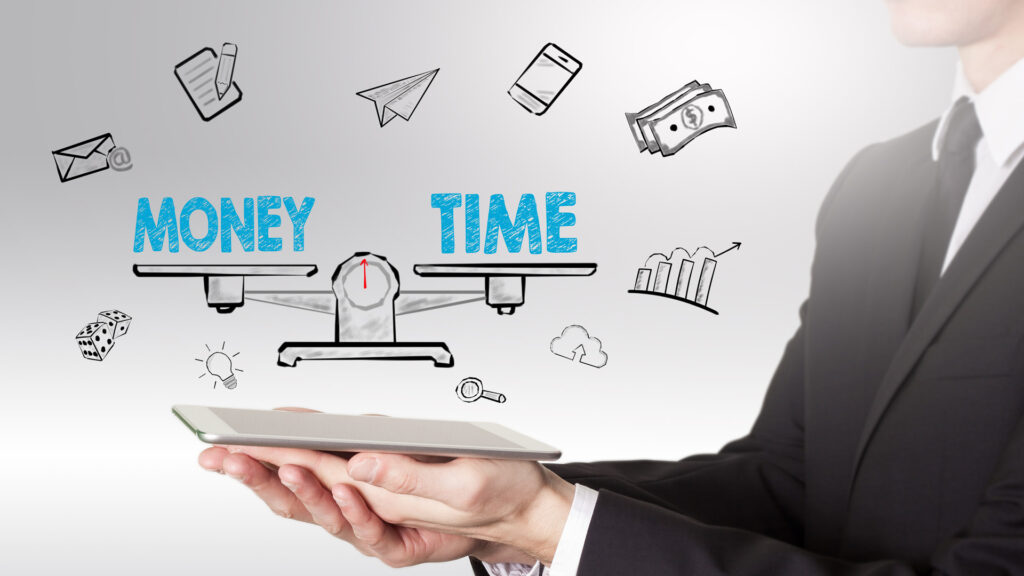
Controlling
Zahlen, Daten, Fakten. Für Sie als Controller spielen verlässliche Daten und Kennzahlen eine große Rolle. Mit Ihnen lässt sich die Entwicklung der einzelnen Bereiche sowie die wirtschaftliche Lage eines Unternehmens messen. Durch umfangreiche Informationen zu den wirtschaftlichen Daten im Unternehmen, die das Controlling liefert, kann das Management beurteilen, ob die Prozesse bei Produktion, Vertrieb oder in der Personalentwicklung auch auf die anvisierten Ziele zusteuern. Kennzahlen und betriebswirtschaftliche Auswertungen sind für die Steuerung eines Unternehmens existenziell.
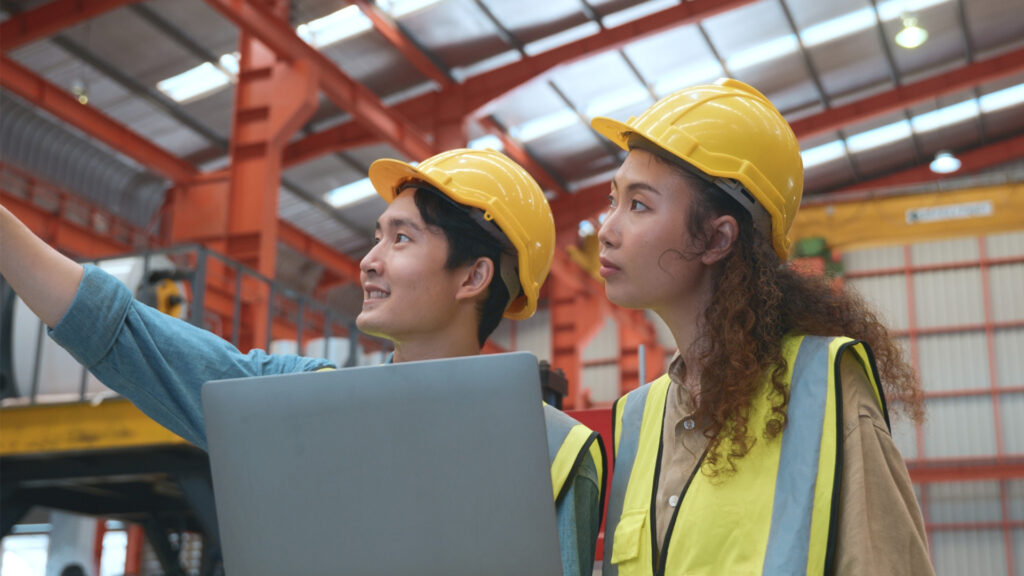
Human Ressources
Schaffen Sie die Grundlage für ein gerechtes Prämien- und Akkordlohnsystem. Neben dem Gebrauch der erfassten Zahlen für genaue Schwachstellenanalyse können Sie die genau erfassten Daten für entsprechende Entlohnungen verwenden. Erfasste Personalzeiten und -leistungen können mit Leichtigkeit in Ihr HR-System exportiert werden.
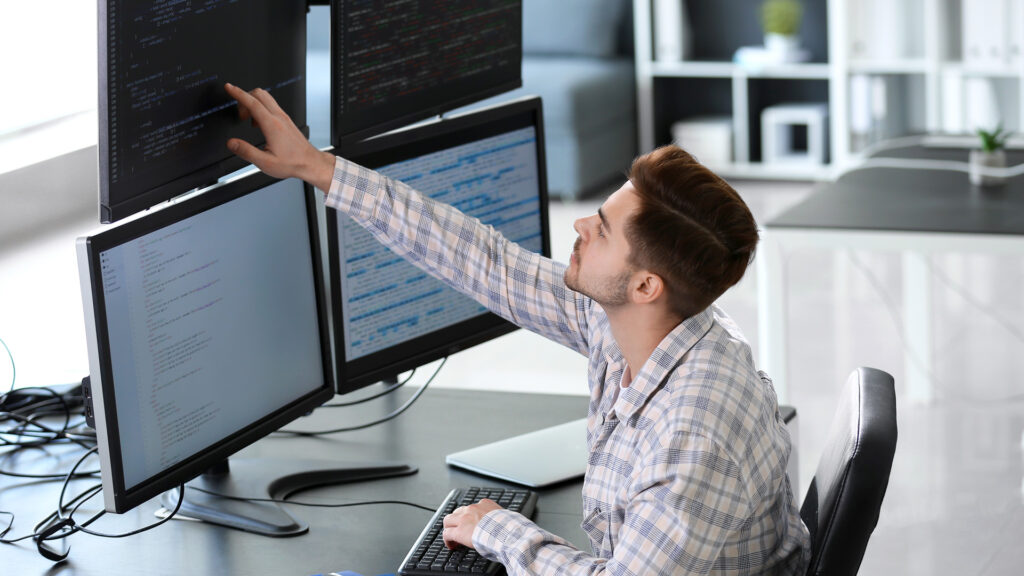
IT – Leitung
Als IT-Leiter profitieren Sie von unserer langjährigen Erfahrung bei der Integration unserer Softwarelösung in Ihr bestehendes IT-Umfeld. Sie haben die Möglichkeit unsere variablen Schnittstellen an die Bedürfnisse Ihrer vorhandenen Softwarelösungen anzuspassen. Profitieren Sie von unserem Know How und führen Sie Lösungen ein, die einfach zu handeln und nicht so Beratungsintensiv sind.
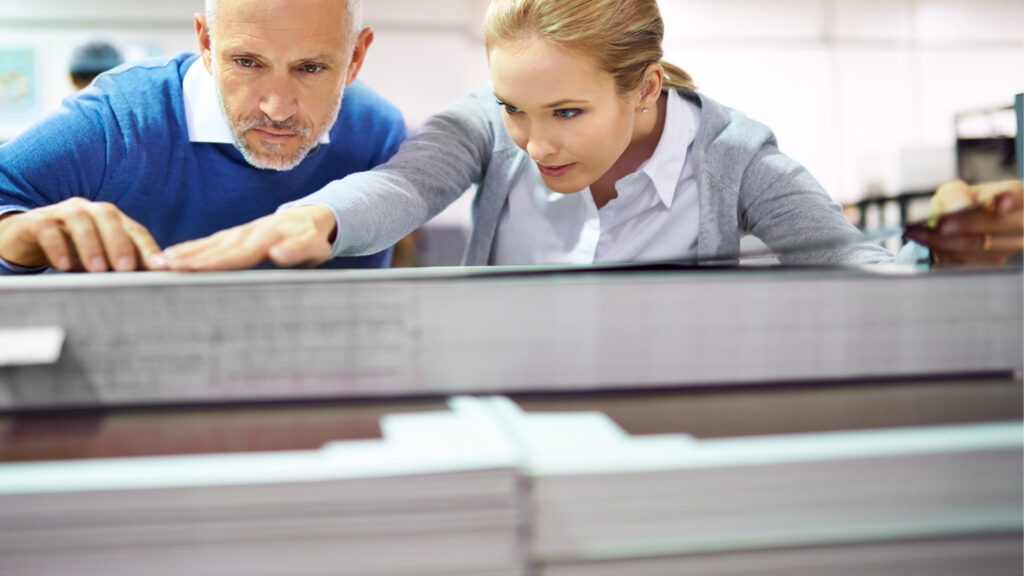
Qualitätssicherung
Sie sind für die Qualität der gefertigen Produkte verantwortlich und müssen diese nachhaltig sicherstellen. Wir unterstützten Sie bei der fortwährenden Qualitätskontrolle. Durch die Integration in die Produktionsprozesse lassen sich Qualitätsprüfungen ereignisbasiert einsteuern und Produktionsdaten mit Qualitätsdaten verknüpfen. Für jeden Produktionsschritt ist nachvollziehbar, wann und an welchem Arbeitsplatz dieser ausgeführt wird.

Meister – Ebene
Unsere Lösung bietet Ihnen die Möglichkeit, Ihre Aufträge und Resourcen entsprechend vorzuplanen und die laufende Produktion im Überblick zu behalten. Durch die Visualisierung der Produktion in Echtzeit, können Sie bei Problemen direkt reagieren. Sie sehen den Produktionsfortschritt und die unterschiedlichen Stillstände der jeweiligen Machine. Schwachstellen können somit erkannt und kurzfristig eliminiert werden. Sprechen Sie mit Ihren Mitarbeitern über Fakten und Sie werden feststellen, dass Diskussionen erheblich minimiert werden.
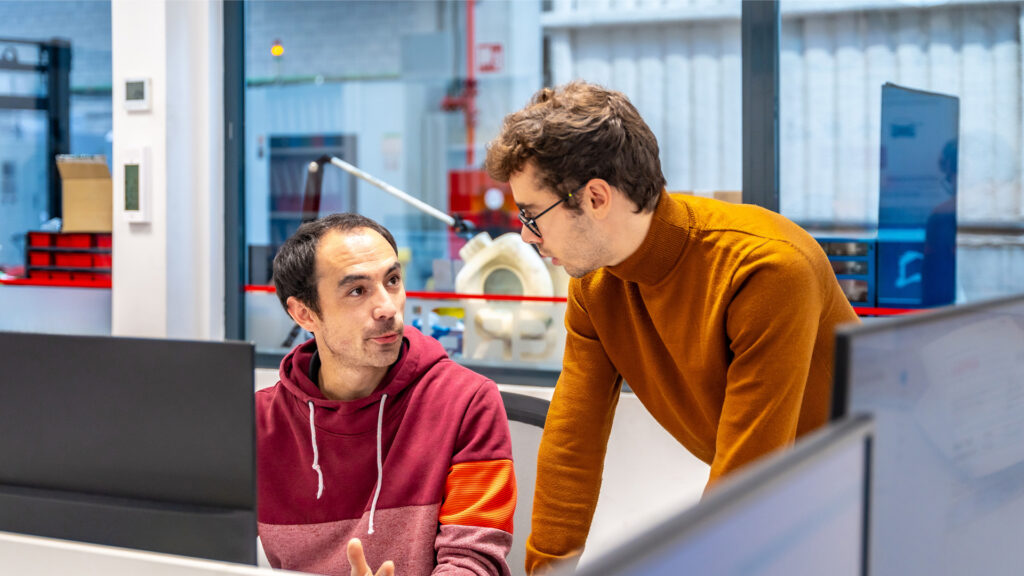
Arbeitsvorbereitung
Kapazitätsplanung ist eines der Hauptaufgaben von Arbeitsvorbereitern/innen. Durch diverse Module, wie z.B. die grafische Plantafel PROplan. Diese unterstützt Sie mit einer ONLINE-Visualisierung aller Maschinenzustände und ungeplanter Ausfälle, die sich evtl. negativ auf den geplanten Liefertermin auswirken. Somit können Sie schnell reagieren und Verzögerungen reduzieren.
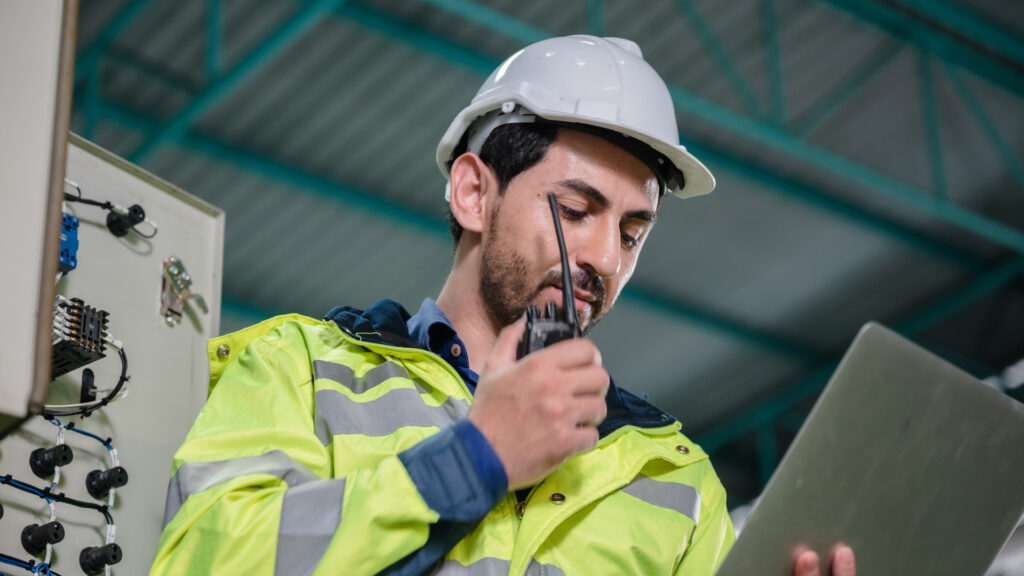
Technik
Neben den produktionsverantwortlichen Mitarbeitern kann sich auch das technische Personal LIVE über das PROview-Modul einen Überblick über alle Produktionsmaschinen und Arbeitsplätze verschaffen. Somit kann bei Maschinenausfällen, wie z.B. bei technischen Problemen an der Maschine, schnellstmöglich reagiert werden. Unnötig lange Stillstände werden somit reduziert und die Produktivität dadurch erhöht.
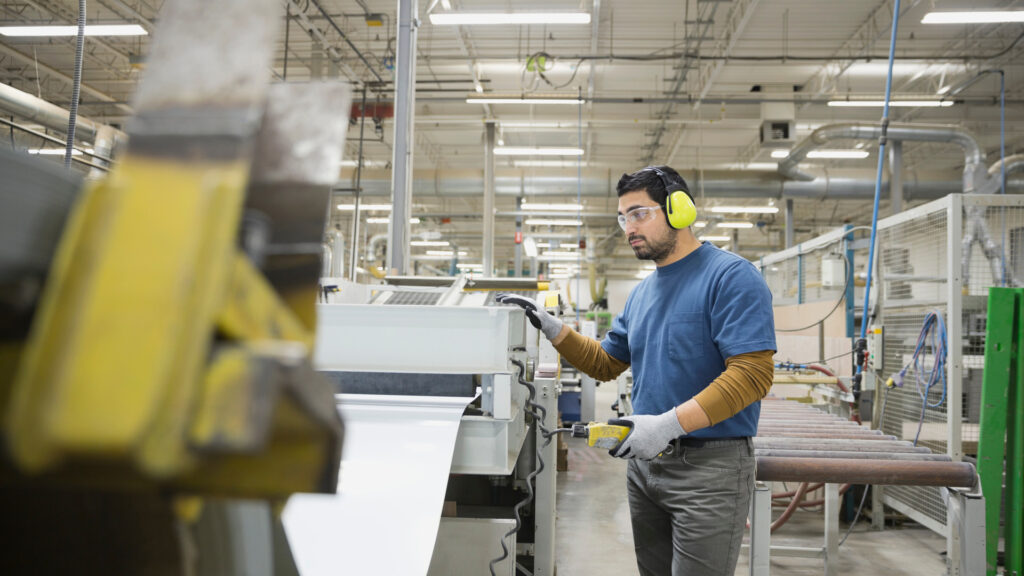
Produktionsmitarbeiter
Intuitiv zu bedienenden Terminals erleichtern jedem Mitarbeiter die Erfassung relevanter Daten und fördern die Bereitschaft dies gewissenhaft zu tun. Auf dem Terminal können Sie sich sowohl Auftrags- als auch Artikelbezogene Informationen anzeigen lassen, was den ersten Schritt in die papierlose Fertigung bedeutet. Sie werden Unterstützung von Ihren Vorgesetzten erhalten, wenn Probleme aufgezeichnet wurden.
Einordnung MES in die Standards und Richtlinien nach VDI 5600
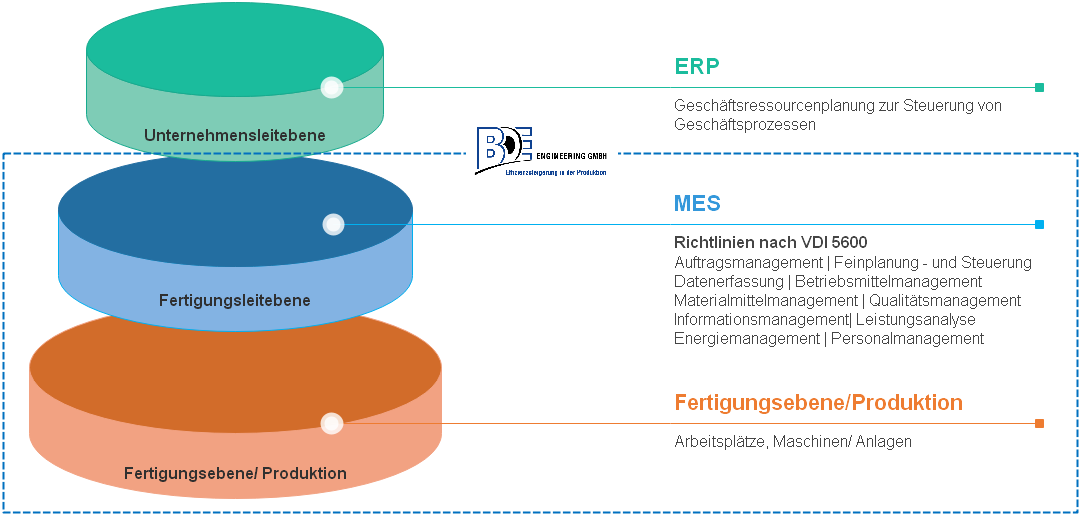
Ihr Nutzen durch MES
So profitieren Sie durch die MES Suite PROefficient: Entdecken Sie die Vorteile unserer MES-Lösungen und optimieren Sie Ihre Produktionsprozesse nachhaltig. Unsere Software und Hardware bietet Ihnen umfassende Kontrolle, Effizienzsteigerung und Transparenz in Ihren Abläufen. Alles, was Sie für eine zukunftssichere Fertigung benötigen.
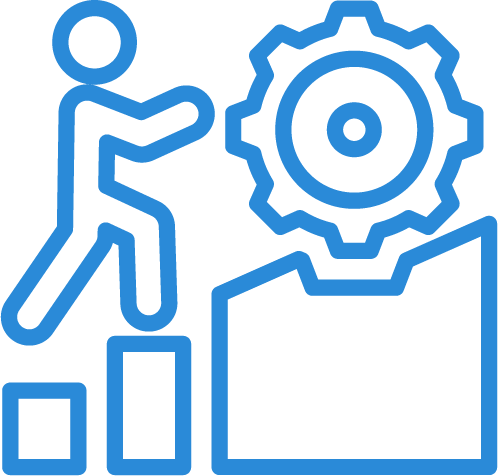
Optimierung der Maschinenauslastung
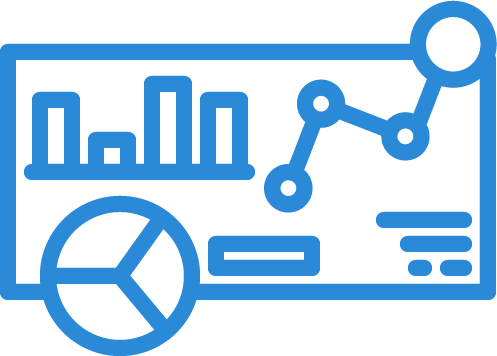
Visualisierung Ihrer Daten
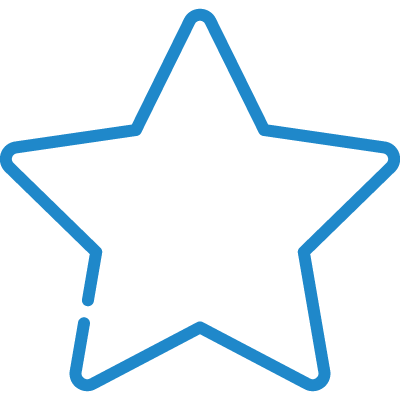
Weniger Suchaufwände
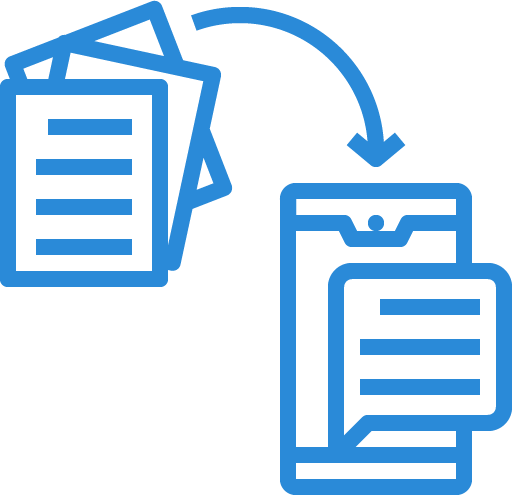
Reduzierung von Papieraufschreibungen
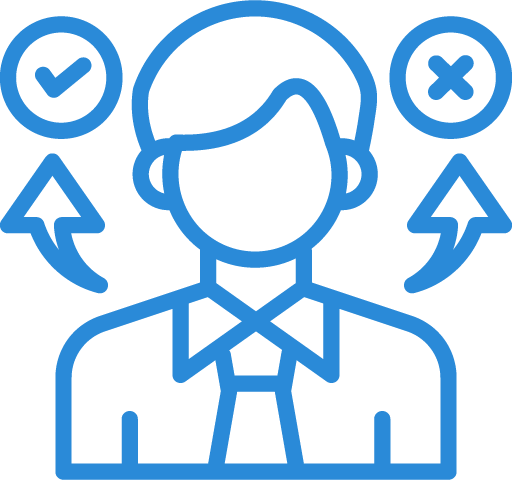
Entscheidungsgrundlage für Investitionen
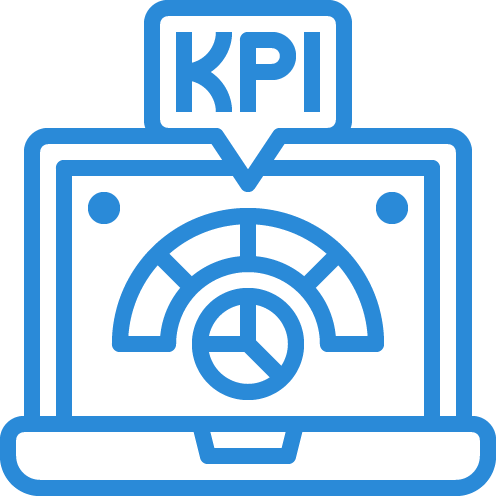
Aussagekräftige Kennzahlen
Tipps zur erfolgreichen MES-Einführung
Profitieren Sie von dem Wissen unserer MES-Experten. Bei der Einführung eines MES-Systems sollten einige grundsätzliche Voraussetzungen gegeben sein und Regeln beachtet werden. Wir geben Ihnen einen kurzen und überschaubaren Überblick und unterstützen Sie gerne bei Ihren weiteren Planungen.
Kurzfristig Termin vereinbaren
Vereinbaren Sie kurzfristig einen unverbindlichen Termin und lernen Sie uns kennen. Wir zeigen Ihnen Lösungen zur digitalen Erfassung und Aufbereitung Ihrer Fertigungsdaten. Sie lernen die wichtigsten Vorteile und Funktionen unserer MES Suite PROefficient kennen. Abschließend ermitteln wir, welche Möglichkeiten zur Effizienzsteigerung in Ihrer Produktion möglich sind.
Wie? Präsentation per Webkonferenz
Dauer? Ca. 60-90 Minuten
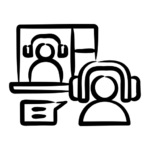